生産管理、製造現場の問題に対する考え方(全体像)
私が事例Ⅲの生産管理、製造現場の問題に対して課題、解決策を考えるうえで整理し、ファイナルペーパーに作成した内容は以下の通りです。
本番もこの内容に従って本番の事例企業に対して何が有効な解決策を提案しました。
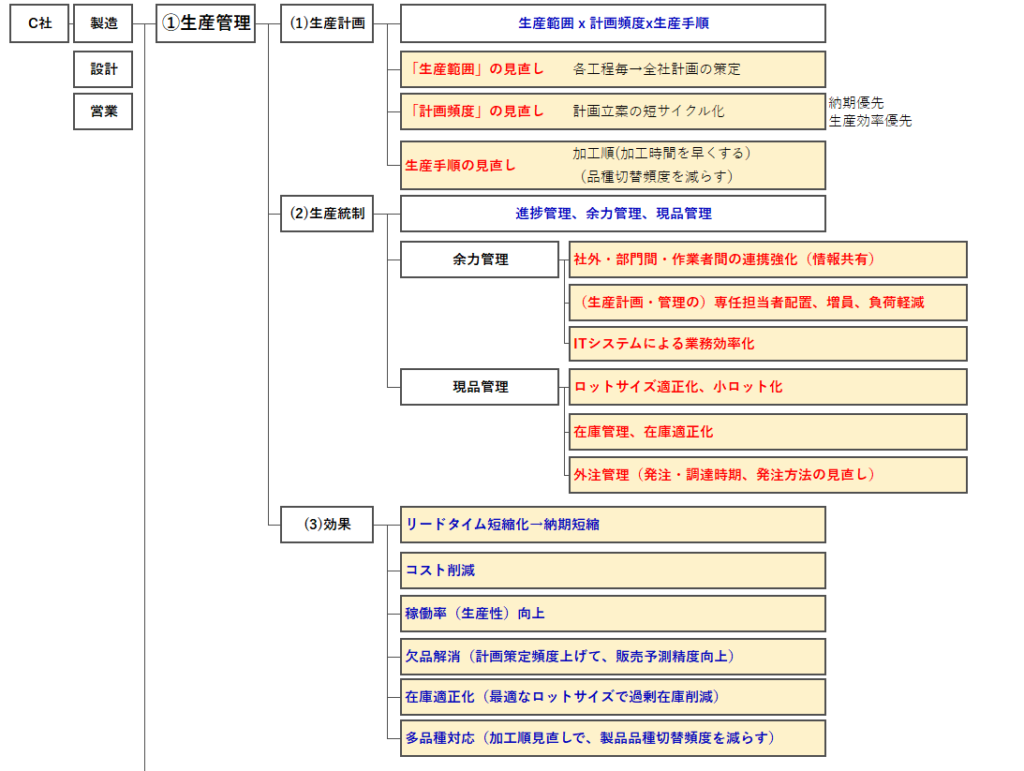
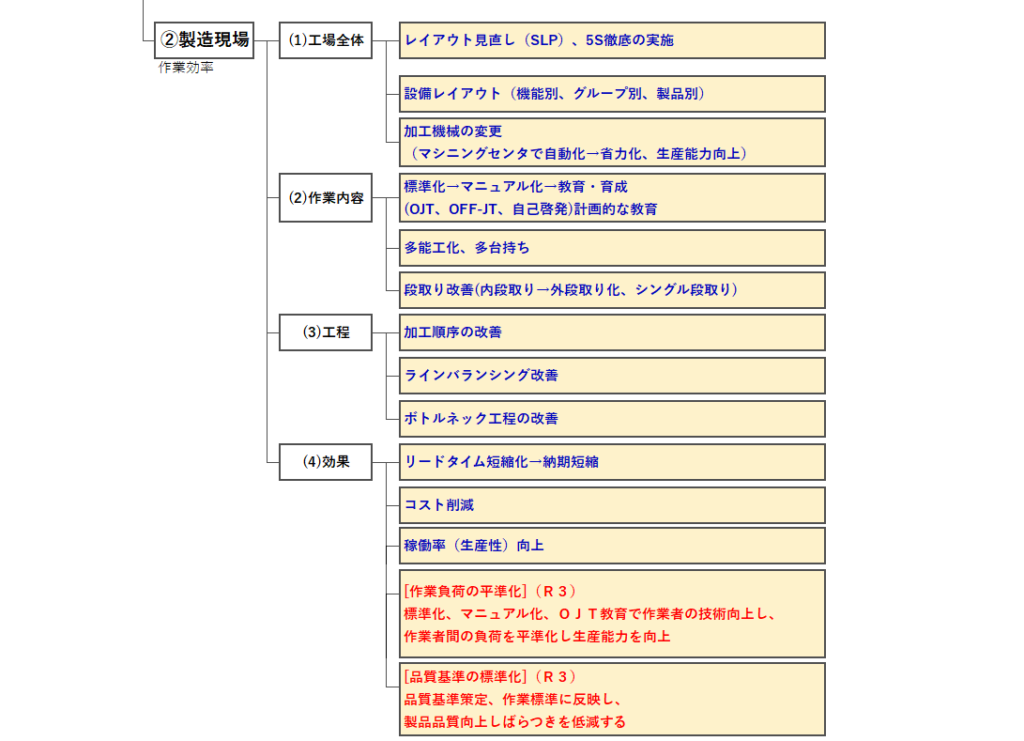
①生産管理の問題、改善策、効果(改善効果)
生産管理に関わる問題は「生産計画」、「生産統制」の2つに起因し、それに対応した改善策を提案する必要があります。
・「生産範囲」の見直し → 各工程毎→全社(全工程)の生産計画の策定にする
・「計画頻度」の見直し → 計画立案の短サイクル化 [納期優先、生産効率優先等]
・「生産手順」の見直し → 加工順を見直す(加工時間の短縮。品種切替頻度減らす)
・「余力管理」の見直し
→社外・部門間・作業者間の連携強化、情報共有
→生産計画・管理の専任担当者の配置、増員、負荷軽減
→ITシステムによる業務効率化
・「現品管理」の見直し
→ロットサイズ適正化、小ロット化
→在庫管理、在庫訂正化
→外注管理(発注時期、調達時期、発注方法の見直し)
・リードタイム短縮化→短納期化
・コスト削減
・稼働率向上、生産性向上
・欠品解消(計画策定頻度を上げて、販売予測精度を向上)
・在庫適正化(適正なロットサイズで過剰在庫を削減)
・多品種対応(加工順見直しにより製品品種切替頻度を減らす)
②製造現場の問題、改善策、効果(改善効果)
次に製造現場に関する問題です。これは「工場全体」、「作業内容」、「工程」の3つに区分しました。
・レイアウトの見直し(SLP)、5Sの徹底
・設備レイアウトの見直し(機能別、グループ別、製品別)
・加工機械の変更(マシニングセンタ導入により自働化、省力化し生産能力向上)
・作業標準化→マニュアル化→教育・育成(OJT、OFF-JT、自己啓発、計画的な教育実施)
・多能工化、多台持ち
・段取り改善(内段取り→外段取り化、シングル段取り)
・加工順序の改善
・ラインバランシング改善
・ボトルネック工程の改善
・リードタイム短縮化→納期短縮、短納期化
・コスト削減
・稼働率(生産性)向上
令和3年の問題ですが、これらを組み合わせて下記のように回答できます。
・作業負荷の平準化
「標準化、マニュアル化、OJT教育で作業者の技術向上、作業者間の負荷を平準化し生産能力を向上」
・品質基準の標準化
「品質基準を策定、作業標準に反映し、製品品質向上させ、ばらつきを低減する。」
さいごに
以上が事例Ⅲの生産管理、製造現場の問題に対するまとめです。
あまり難しく構造化するのではなく、本番の80分の中で瞬発力高く頭の中から直ぐに引き出せるようにすることが重要です。
次回はIT問題に関する内容です。
コメント